L’industrie face aux défis énergétiques
Dans un monde où les consommations énergétiques sont de plus en plus suivies et la stabilité énergétique est mise à l’épreuve par une multitude de facteurs, il est essentiel de comprendre le rôle crucial que jouent les données dans la construction d’une résilience énergétique durable. Les données sont devenues le pilier central sur lequel repose la capacité des entreprises à anticiper et répondre aux défis industriels et l’optimisation énergétiques en fait bien partie.

La résilience énergétique dans l’industrie se traduit par la capacité des entreprises à maintenir, voire réduire un approvisionnement énergétique fiable et à s’adapter efficacement aux perturbations et changements dans le système énergétique.
Les stratégies possibles d’optimisation et d’adaptation pour une résilience énergétique comportent nécessairement :
- L’adaptation du système par la diminution (ou suppression) des émissions de carbone en modifiant les filières d’approvisionnement de matières premières et en privilégiant l’utilisation d’énergies à faible empreinte carbone (hydroélectricité, nucléaire, biomasse,…).
- L’amélioration de l’efficacité des procédés par le développement de procédés industriels innovants moins émetteurs de gaz à effet de serre.
- l’optimisation de l’utilisation de l’énergie dans les processus industriels en identifiant et en réduisant les sources de gaspillage grâce à des mesures appropriées (consommations liées au process ou aux déperditions, on parle d’efficacité énergétique.
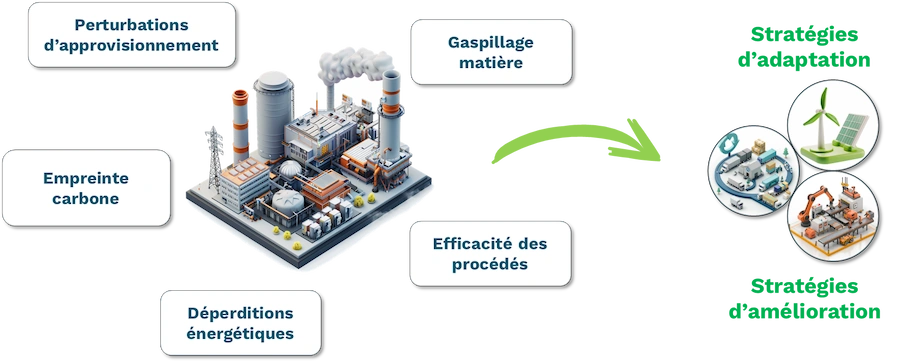
L’amélioration de l’existant constitue le premier levier d’amélioration. Il est primordial d’identifier les inefficacités et les opportunités d’amélioration qui sont souvent disponibles plus rapidement et à moindre coût. Le premier levier est l’amélioration des process de fabrication par l’optimisation de la consommation énergétique à iso-qualité.
Pour répondre à ce besoin, deux types de solutions existent. Le premier consiste à mettre en place des solutions techniques (mécaniques) comme la pose de carters pour assurer un maintien de température, permettant donc un bouclage de l’énergie. Le second s’intéresse davantage à l’exploitation de données pour permettre une analyse plus fine des étapes du processus de production. Nous allons particulièrement aborder ce deuxième type de solution. L’objectif est de mettre la donnée au service de l’analyse de la performance.
Une fabrication à la juste qualité
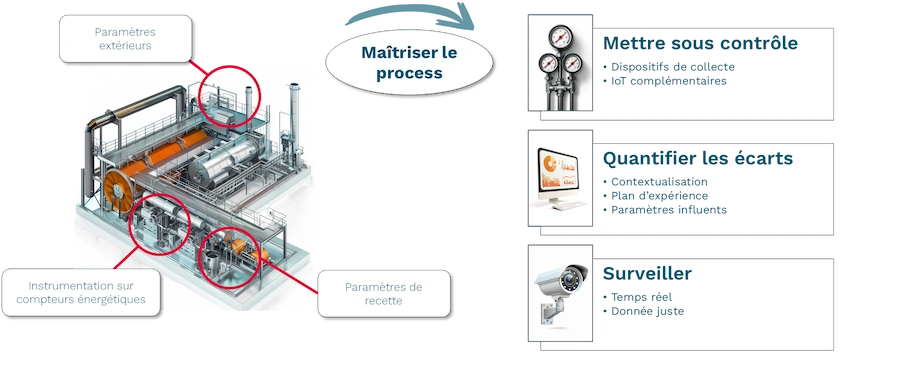
Pour s’assurer d’une analyse fine de son niveau de qualité, il est nécessaire de mettre sous contrôle son process, par une instrumentation au niveau machine de la manière la plus fine possible.
Cette mise sous contrôle de son procédé permet de comprendre et de quantifier les écarts par une collecte de l’information, la traçabilité de sa matière et le suivi de ses rebuts. La maîtrise de la qualité (écart type de variabilité des paramètres) permet de tendre vers la limite basse de l’intervalle et de tendre vers l’économie d’énergie, notamment pour les industries énergivore (exemple : fabrication ciment, fabrication papier, …).
De plus, en surveillant en temps réel les performances des équipements et en mettant en place des alertes préventives, nous pouvons détecter les dysfonctionnements potentiels et les inefficacités dès qu’ils se produisent, ce qui nous permet d’intervenir rapidement pour minimiser les pertes d’énergie et optimiser les performances globales du processus de fabrication.
Une réduction des temps de démarrage
L’idée est, lors de changement de campagnes, de converger plus rapidement vers la cible pour réduire le temps de setup et ainsi gagner en énergie et également en productivité.
Prenons l’exemple d’un fabricant de tablette de lave-vaisselle.
Afin d’assurer une utilisation optimale au client final, le fabricant doit s’assurer que ses tablettes possèdent une dureté comprise au sein d’un intervalle de tolérance. Lors des changements de campagne, de nombreux produits hors tolérance sont alors rebutés, présentant une perte conséquente.
L’analyse des paramètres a montré que la mesure de la dureté dépend, entre autres, d’un paramètre d’environnement à savoir l’hygrométrie. Il est donc nécessaire de contextualiser et de prendre en compte les données extérieures à la ligne de production elle-même.
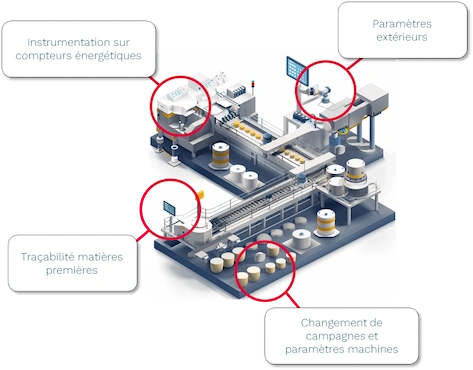
En examinant de près les données de performance des équipements, comme les températures de fonctionnement, les niveaux de consommation énergétique et d’autres paramètres pertinents, nous pouvons identifier les paramètres influents à l’atteinte du régime nominal.
Avec le changement climatique que nous connaissons, les saisons se transforment et les variations de températures s’amplifient. Dans cet exemple, il est donc nécessaire d’intégrer une analyse de ces paramètres au sein d’une intelligence opérationnelle pour avoir un paramétrage optimum et limiter la montée en cadence de la machine.
Soutenir la transition par l’intégration technologique et applicative
Qu’il s’agisse d’un travail axé sur la qualité ou sur la montée en cadence des lignes de production, les données jouent un rôle central en permettant d’analyser finement chaque étape du processus de production et d’en déterminer les paramètres influents.
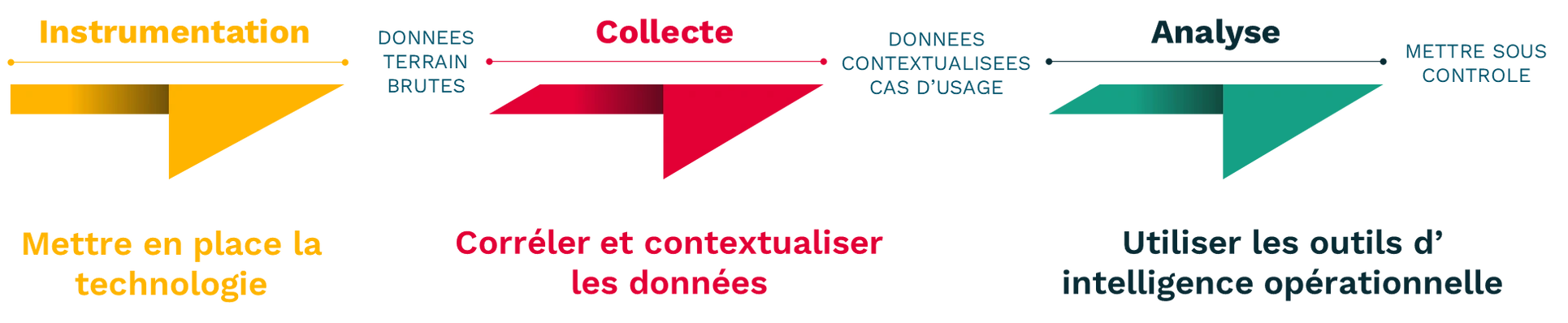
La transition doit s’effectuer sur trois axes :
- L’instrumentation : En intégrant les capteurs IoT et d’autres dispositifs de collecte de données au système de contrôle commande, les entreprises peuvent recueillir des informations précieuses sur la consommation énergétique, la production, les temps d’arrêt et d’autres paramètres pertinents en temps réel.
- La collecte de données et la contextualisation : Contextualiser l’ensemble des données du process mais également les données « extérieures », les données matière et qualité, par une agglomération des données des différentes sources.
- La mise en place d’outils intelligents : Le déploiement d’outils d’analyse de la donnée doit se faire par un travail collaboratif avec le métier pour apporter un suivi et une aide à la décision en fonction des cas d’usage.
Cette démarche apporte une compréhension du process, une contextualisation des données collectées et une mise en évidence de leurs impacts sur le système pour optimiser les conditions opératoires.